The charts project the social impact parameters of the CSR project for which social return on investment (SROI) will be measured upon completion.
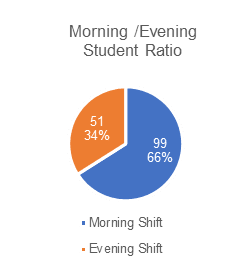
GreyOrange has partnered with an NGO, Turn Your Concern into Action (TYCIA) and Yatan, through its flagship program Pathshala charitable learning centers. The mission of Pathshala is to revive education in the lives of lower-income children from migrant families living in Gurugram and Delhi. The objective is to enable children who have never attended school or have dropped out of the educational system due to the pandemic to progress to their age-appropriate learning levels and enter mainstream government schools.
In 2021 we opened our first Pathshala school and are in the process of launching another. The center runs afternoon classes, extracurricular activities and development sessions for students, and assists with student ID card formation and admission process documentation. Most students (66%) attend the morning shift and 34% go to the evening shift. There is a high level of gender diversity, as 47% are girls and 53% are boys, reflecting attendance that is at or near gender parity.
To ensure that we are making a meaningful difference, GreyOrange measures our social return on investment (SROI). The SROI of our work is determined not only by the percentage of students who go on to attend mainstream schools, but also the amount by which their earnings are projected to exceed the minimum wage, which they otherwise would have been likely to earn. Among total students attending the Pathshala school, we have enrolled 20% into mainstream schools in 2022, reflecting an SROI of $12. However, we believe we are on target to achieve our objective of enrolling at least 90% of the students in mainstream schools after they graduate from the program, resulting in an SROI of $36.
The charts project the social impact parameters of the CSR project for which social return on investment (SROI) will be measured upon completion.
The charts project the social impact parameters of the CSR project for which social return on investment (SROI) will be measured upon completion.
The charts project the social impact parameters of the CSR project for which social return on investment (SROI) will be measured upon completion.
All GreyOrange solutions are designed and produced in compliance with global Autonomous Mobile Robot standards and OSHA guidelines. Our state of the art production facility complies with UL standards and environmental safety norms reducing lead times and helping customers deploy solutions faster to reduce effort and save money.
RoHS: GreyOrange solutions reduce the environmental effect and health impact of electronic equipment by being compliant with the RoHS 3 (EU Directive 2015/863).
Parts’ source tracking: GreyOrange has dedicated systems in place to track the components used in our systems back to the source. This results in higher quality products, continuous improvement, and the ability to track and optimize carbon footprint throughout the supply chain
Supplier and vendor onboarding practices: Sustainable sourcing is the cornerstone of environmental stewardship and sustainability values are an integral part of the GreyOrange vendor selection criteria. We also work closely with our suppliers to help them improve their processes and reduce environmental impact
Robot Power Consumption: GreyOrange robots are optimized to reduce active power consumption as follows:
Lithium batteries: Robots in GreyOrange solutions use lithium batteries, unlike the lead acid batteries used in standard warehouse equipment like forklifts that are not environment-friendly. In addition, smart charging algorithms ensure that the power level of batteries always stays in the healthy range to maximize battery life.
Designed to reduce energy in the warehouse: The US Energy Information Administration study shows that up to 75% of warehouse energy consumption is due to lighting and heating. GreyOrange deployments can work without lighting and air conditioning. These solutions reduce the warehouse’s energy consumption and are a great fit for dark warehouses.
Reduced area: GreyOrange solutions can help reduce the operational area by up to 80% thereby decreasing the energy requirements that would have stemmed from the larger operational area as well as a reduction in material required to construct the warehouse area as well.
Reprocessing of orders: Manual operations are prone to errors which could result in high resource consumption in the form of having to process the orders again as well as restock returned items. Automated solutions from GreyOrange help improve accuracy up to 99.9% resulting in fewer reprocessing of erroneous orders thus saving resources and ensuring a more sustainable operation.
Packaging optimization: GreyOrange pick-to-pack flows allows retailers to ensure the best packaging utilization for their orders ensuring a reduction in packaging material requirements as well as optimized transportation capacity leading to a reduction in fuel consumption for logistics
Increasing warehouse lifetime: A higher efficiency to the tune of 200% – 500% achieved by GreyOrange solutions mitigates the need to move to a newer warehouse and decommission older facilities which would otherwise lead to a high environmental impact
Maximum Life Robotics and Repair first approach:
“Our planet’s survival will depend on how well we retain the value of products within the system by extending their life” – Joyce Msuya, UN Environment Acting Executive Director
Battery disposal: GreyOrange trains its maintenance personnel to handle batteries safely and help with disposal to the registered recyclers / designated collection centers. This reduces the dependency on these materials, improves the security of the supply chain, and reduces the human and environmental impact brought by these batteries
Contact UsSince 2019 GreyOrange has reduced its overall energy consumption by 11% and its water consumption by 5% as well. A continuous effort has been made to optimize our operations and drive energy-saving campaigns and programs running continuously across our global operations. Examples include
Energy saving in our facilities: At Greyorange we are always working on energy conservation efforts that are leading to a reduction in energy consumption and has implemented many energy-saving initiatives.
We are getting regular third-party energy audits for energy efficiency improvement throughout the company including installing motion sensors, a capacitor bank for maintaining the power factor, UPS relays for lights, implementation of LED lights as well as installing transparent sheets in the ceiling for daylight and insulation within the ceiling.
IT and data center energy savings: GreyOrange leverages the most efficient energy savings programs by utilizing a third-party provider to host our applications and data center in the cloud. We also implement wide-ranging data storage optimization programs to archive data after defined periods and automatically launch backups
Water consumption: GreyOrange reuses or recycles 62% of the water in all its facilities leading to a reduction in water consumption by 5% since 2019.
We have changed our packaging from wooden and nail packaging to cardboard to reduce the waste at our customer’s end. We use reusable packaging to get some of our raw materials from our suppliers to support our waste reduction initiatives and are reducing our internal rejection to make sure we are lowering our waste generation.
Our biodegradable waste is being composted and used for the plantation which ensures waste reduction, and resource optimization.
We partner with NGOs and organize events including local cleanups to make the earth a greener place.
On different occasions, we distribute green gifts to our employees, which helps create awareness and contribute to the development of the ecosystem of green gifting.
We use 100% electric forklifts and stackers that run on batteries to eliminate direct emissions.
GreyOrange is a purpose-driven company proud of our authentic “solver” culture where every voice is valued. Working together we are doing our part to create a better world through both environmental and socially conscious investments and practices.
We extended care and support to employees through the global pandemic. For example, in our Gurgaon, India facilities we ran free vaccination camps for our employees and families which proved a resounding success, and efforts will continue to administer the vaccine as long as the COVID-19 variant continues to spike. Our quarterly “Thrive” long weekends encourage employees to relax, rejuvenate and spend time with their loved ones and provide dedicated allowances for wellness needs.
We are a work-from-home (WFH) company. Adopting the WFH model reduces our carbon footprint by reducing fossil fuel usage and energy consumption during commutes. WFH saves employees’ time and energy that they otherwise would have expended during travel. As a result, our workforce can dedicate that energy to enhance their well-being through time spent with loved ones and engaging in exercise and other health-producing activities.